When it comes to endless splicing, the most frequently asked questions we get involve recipe management – specifically, “How do I develop a new recipe?” or “How do I know when I have the right pressure set for the type of belt I am using?” or “Should I increase or decrease my temperature if my tips aren’t filled?”
We decided that a blog would be the perfect way to address some of these questions with proper recipe tips. But this can’t all be covered in one blog. So this week, I’d like to focus on where to begin and how your belt type affects your recipe.
Where Do You Start?
Let’s face it … developing a new splice recipe can be a challenging process – especially when there’s insufficient technical information available. Experienced belt fabricators know that a recipe for a given belt will often work on one type of splice press, but not another.
Many conveyor belt manufacturers provide technical datasheets; however, these guidelines often do not account for all splice presses used in the industry. In those situations, having a proven and methodic approach to developing an endless splice recipe can save a lot of time and money while optimizing the splice quality.
Splice Recipe Variables
The good news is that there is no one right answer when developing a splice press recipe for a new type of conveyor belt. Different combinations of temperature, pressure, and dwell time can be used to achieve similar splice quality levels. However, knowing where to start and how to troubleshoot the splice results will help you make the right adjustments to splice parameters to quickly find the optimal splice recipe.
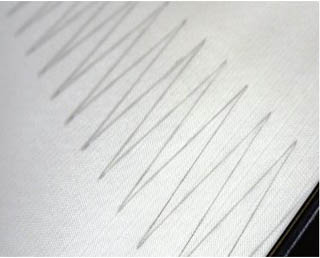 |
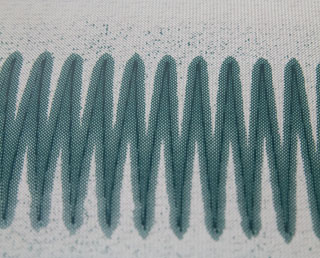 |
Proper Bleedthrough |
Excessive Bleedthrough |
Let’s begin with a common example:
You notice the tips of the fingers in an endless splice aren’t filled, yet there’s bleed-through on the back of the belt. Should the splice temperature be increased, or pressure setting be decreased, or maybe both? What about dwell time? Should it be increased or decreased? Maybe preheat should be used, or maybe the top half temperature should be increased and the bottom temperature decreased?
These are the primary input variables that belt splice technicians consider when drawing on their experience to create that working splice recipe – but there are other factors that must be considered. We’ll break it down here, beginning with the type of belt you are joining.
PVC and Polyurethane – How They Process Differently
The type of belt is a major consideration when developing your splice recipe because each belt reacts differently to heat. For example, PVC transitions more gradually from a solid to a liquid state than Polyurethane (or TPU). Often, technicians incorrectly use excessive splice pressure – rather than increasing splice temperature – which can lead to defects and inconsistent splice quality with the same belt and recipe. In many cases, the ideal endless splice can be obtained by increasing splice temperature for PVC belts and decreasing splice pressure. These two easy adjustments can significantly reduce this variation in splice quality caused by the excess pressure applied otherwise.
Another important difference is melt viscosity, which is the rate at which plastic flows at a given temperature. Polyurethane has a lower viscosity than PVC, so it flows easier than PVC. One analogy of this is that liquid Polyurethane flows like water, whereas PVC flows like molasses. As a result, less pressure is needed when splicing Polyurethane belts. So, in general a Polyurethane belt requires a lower splice temperature and lower pressure than PVC belt.
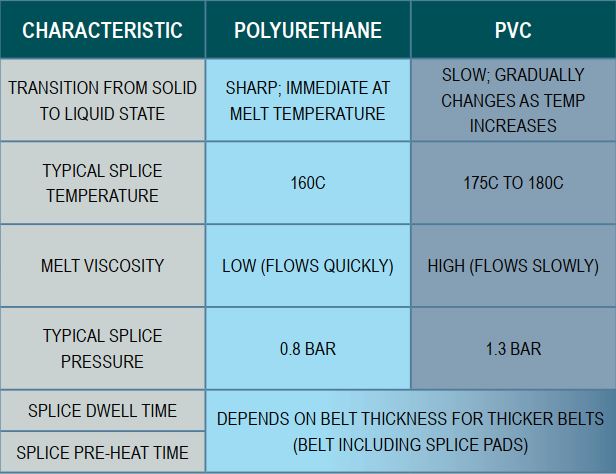
Next week, we will focus on the fundamentals of belt splice recipe development – temperature, pressure, and time – and what part they play in achieving a strong, consistent endless splice. Stay tuned!
Authored by: Michelle Graves, Product Manager
Graves manages the overall global business, market plans, technical support, and activities associated with the light-duty belting market for the Novitool® product line, including new product development, market analysis, and global strategy. Graves holds a bachelor’s degree from Albion College as well as a master’s degree from Grand Valley State University.