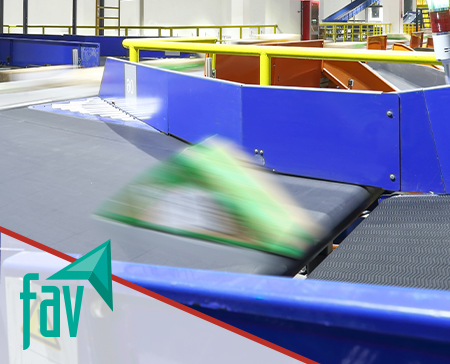
Accumulating Value
$23,640
Industry
Logistics
Product
Hitch Guards & Segmented Transfer Plates
PROBLEM
A major parcel logistics company was experiencing some dangerous conditions at the conveyors of one of their major airport hubs. Daily product jams at the hitch and transfer of one conveyor were resulting in accumulated product rubbing up against the belt. As more and more product began to build up, it created friction on the belt, and melting occurred, resulting in a fire hazard and unscheduled downtime. Additionally, foreign object debris would get trapped in between the belt and the hitch cover, causing damage to the belt itself. Service teams had to reach inside the hitch area and risk injury.
SOLUTION
While working at another location within the company, the Maintenance Engineering Manager had seen Flexco Hitch Guards and Segmented Transfer Plates in action. So when he noticed a similar issue at his new air hub location, he jumped at the chance to use both as a quick and easy solutions to his safety and package jamming problems.
RESULT
Installation of the Hitch Guard at the hitch point and Segmented Transfer Plates was easy with the help of the installation kits. Once installed, results were immediate, with package jams eliminated and reduced safety risks for the employees thanks to the bright yellow color of the guard and segments bringing attention to the gaps. No product jams or debris rubbing on the belt means the maintenance team can reduce their budgeting for new belting because the life of the belt is extended. Productivity was increased to standard levels with no packages missing or damaged at the transfer points, which also reduced the risk of injury around pinch points. The site mechanics can now focus their time on more proactive fixes around the conveyor facility, instead of the current interruption of package jams and related belt damage.
The hub estimated a $32/per envelope downtime cost. With an average of 10 jams per week at 52 weeks per year, that meant $16,640 in lost revenue per year. Add to that the cost of manpower – 2 technicians at $25/hour working ½ hour/day at 280 days/year – at $7,000/year, and you have a savings of $23,640 in the elimination of unscheduled downtime and package loss on only one conveyor line.
What Does Flexco Accumulating Value Mean?
When you see the Flexco Accumulating Value (FAV) icon, you can expect a Real-Life Result that represents the measurable, repeatable value added to an operation through its investment in a Flexco solution.
FAV results document the ongoing dollar value realized with implementation of Flexco products or services and details how that value helps operations achieve and maximize their productivity, efficiency, throughput, output, and uptime.